Get All of Your Mobile Medical Surveillance Testing at One Place
OMY is now Worksite Medical! Schedule NowLearn More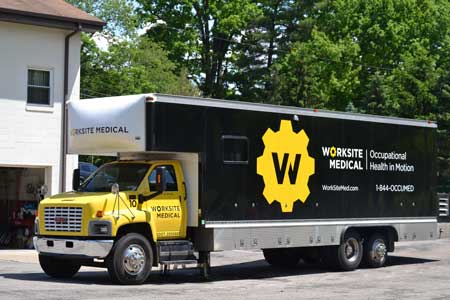
Mobile Medical Surveillance Testing
Do you need mobile medical surveillance testing at your job site?
Do you need a solution that fits both your budgetary and scheduling needs?
Are you looking for more than just audiometric testing?
If you answered “yes” to any or all of these questions, then we’re here to help you with mobile medical surveillance testing!
OMY is Worksite Medical – What’s Changed?
More Options
Using multiple companies to complete your mobile medical surveillance testing services takes more time, and costs more money. Now, you can get everything from audiometric testing & OSHA physicals to blood work, drug testing, and respirator fit testing all at one time, with one company!
A Larger Fleet
Need a lot of testing done at one time? Do you have several job sites that require testing? We can cut down on on-site time with more mobile medical vehicles, and cover every job site, when you need it! Our experienced medical team will complete your testing and maintain all of your records. We’re here to make the entire experience easier and more convenient for you!
A Greater Coverage Area
With deployment sites in Cincinnati, Pittsburgh, York, and Baltimore, we now cover an even greater geographical area. Whether you’re in Detroit or Raleigh, we’ve got you covered! Check out our coverage map HERE
What Our Customers Say
It worked very well for us and did not take away from our production time. Things moved smoothly with no known problems. Your people worked well with our employees and were very professional and courteous.
Best idea since sliced bread. Worksite Medical saved us a lot of time and money, with no compromise in service or care. We will be using your services again.
Our service providers were on time and kept on schedule. We even completed way prior to estimated time. Staff was friendly and kind to our staff. Way to go Worksite Medical!
Ready to Get Started?
If you’re an OMY customer and you want to learn more, we’re excited to talk with you about your mobile medical surveillance testing needs. And we’ve still got York covered, so you won’t need to look at locations that aren’t local to you! Even if you’re not a former OMY customer, and you’re in need of occupational medicine services, we’re ready to help!
Click the button on the right to request more information and/or your free quote today!
Ready to schedule? Just scroll down and complete the short form below, and we’ll get everything started!
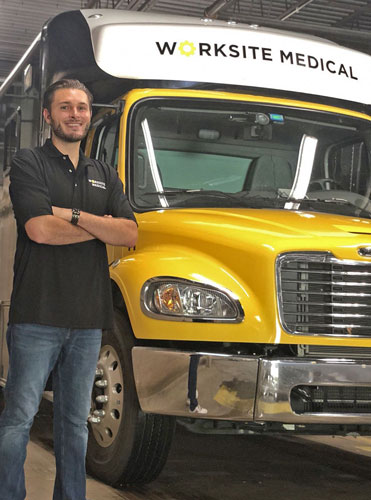
Request a Quote or Schedule Your Mobile Medical Surveillance Testing